Timfoilhat
Time is my accomplice
2A Bourbon Hound 2024
2A Bourbon Hound OG
Benefactor
Life Member
Multi-Factor Enabled
Set up new Hornady 7.5x55 swiss dies. I lube every case by hand with Imperial sizing wax and a bit of mica in the case mouth. The case slides into the die easy enough, pops the primer out, and on the removal stroke it sticks bad. It will ultimately pull through with way too much effort. We've reached the limit of my experience. I'm not sure if this is a die problem, a Hornady problem, or a brass problem.
I've heard that 7.5x55 brass likes to be anealed, some (random internet people) even say after the every firing. I'm wondering if that's the likely issue. My other dies are all Forster, RCBS or Redding... so I don't know if this is perhaps typical of Hornady...I doubt it...but the other cases on my different dies all move through like butter.
I did complete the set up of the seating die and everything's working as it should. There's good neck tension on the bullet as measured with my informal method of sticking the round in my inertia puller and giving the bench 30 whacks. It barely moved. The seating went exactly as I would expect it to go. No bulges or kinks in the brass. The finished product chambers and ejects effortlessly.
PPU brass
Thoughts?
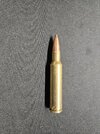
I've heard that 7.5x55 brass likes to be anealed, some (random internet people) even say after the every firing. I'm wondering if that's the likely issue. My other dies are all Forster, RCBS or Redding... so I don't know if this is perhaps typical of Hornady...I doubt it...but the other cases on my different dies all move through like butter.
I did complete the set up of the seating die and everything's working as it should. There's good neck tension on the bullet as measured with my informal method of sticking the round in my inertia puller and giving the bench 30 whacks. It barely moved. The seating went exactly as I would expect it to go. No bulges or kinks in the brass. The finished product chambers and ejects effortlessly.
PPU brass
Thoughts?
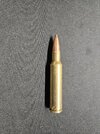
Last edited: